Sydney Business Insights, Kai Riemer and Sandra Peter
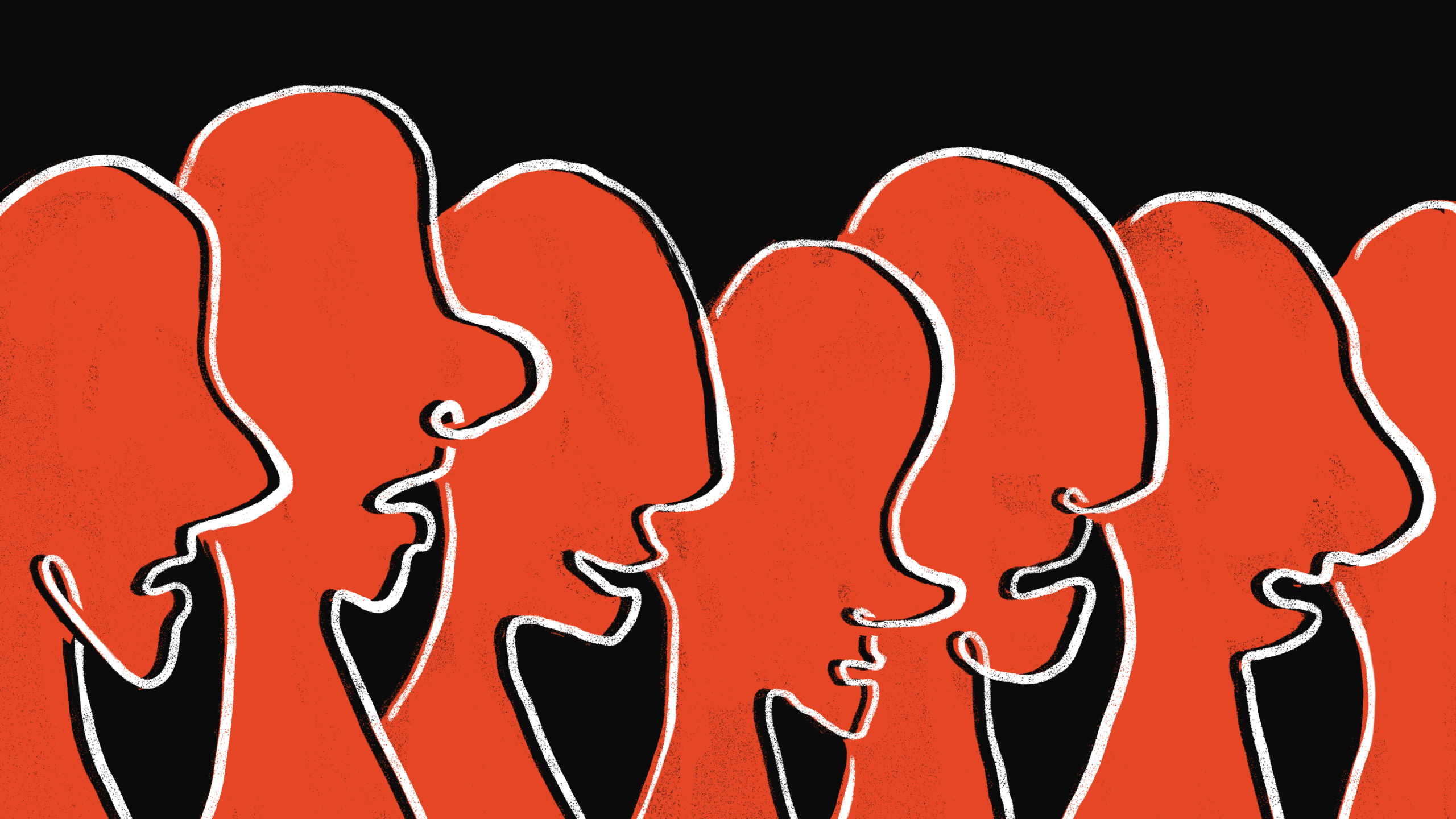
Materialising the digital
Out of Hand: Materialising the Digital at the Powerhouse Museum explores the increasingly important role of digital manufacture in contemporary art, science, fashion, design and architecture.
Show notes and links for this episode
Out of Hand: Materialising the digital Powerhouse exhibition
You can subscribe to this podcast on iTunes, Spotify, Soundcloud, Stitcher, Libsyn, YouTube or wherever you get your podcasts. You can follow us online on Flipboard, Twitter, or on sbi.sydney.edu.au.
Sydney Business Insights is a University of Sydney Business School initiative aiming to provide the business community and public, including our students, alumni and partners with a deeper understanding of major issues and trends around the future of business.
Kai Riemer is Professor of Information Technology and Organisation, and Director of Sydney Executive Plus at the University of Sydney Business School. Kai's research interest is in Disruptive Technologies, Enterprise Social Media, Virtual Work, Collaborative Technologies and the Philosophy of Technology.
Dr Sandra Peter is the Director of Sydney Executive Plus at the University of Sydney Business School. Her research and practice focuses on engaging with the future in productive ways, and the impact of emerging technologies on business and society.
Share
We believe in open and honest access to knowledge. We use a Creative Commons Attribution NoDerivatives licence for our articles and podcasts, so you can republish them for free, online or in print.
Transcript
Sandra Peter Introduction: 3-D printing, dresses, jet engines, bones, buildings, coral reefs, cups and carpets... In a special edition on technologies disrupting the traditional manufacturing process, we go to the Powerhouse Museum to check out the Out of Hand: Materialising the Digital exhibition.
Introduction: From the University of Sydney Business School this is Sydney Business Insights. The podcast that explores the future of business.
Sandra: Recently The Future, This week team went to Out of Hand an exhibition exclusive to the Powerhouse Museum in Sydney that was curated by the Museum of Applied Arts and Sciences and the Museum of Arts and Designs in New York.
Kai Riemer: We interviewed Matthew Connell, the Principal Curator, who put together this exhibition that looks into new forms of manufacturing 3-D printing technologies and its application in a wide range of fields.
Matthew Connell: I'm Matthew Connell, I'm the Principal Curator here at the Museum of Applied Arts and Sciences. I led a team that curated this exhibition Out of Hand: Materialising the Digital. It's about digital manufacturing technologies and how artists and designers and scientists are using those technologies. I'm very interested in the discussions around what people think of the possibilities of digital manufacturing of course 3-D printing being the one that seems to get the most attention.
Sandra: So we thought this was a particularly important exhibition if we want to have a real look into the future of manufacturing and what new technologies can bring to this process. The exhibition showcases over 90 artworks, objects and they use digital technologies and best practices from around the world and you've got everything from 3D printing, to digital knitting, to all sorts of technologies disrupting the traditional manufacturing process not only involving a variety of industries.
Kai: You've got furniture that looks like water. They have carpets very nicely done. 3D printed racers that are powered by a Bosch 18 volt drill, bikini's, fashion items, jet engines.
Sandra: Skulls, ancient statues, cups and saucers designed 200 years ago but never produced.
Kai: Now 3D printed artificial reefs.
Sandra: All of this on display and allowing you an opportunity not only to experience these technologies but also to discover and consider how their applications will impact not only the future of business but our lives in general.
Kai: So there's obviously more than we can cover in one podcast but let's look at a few significant ones. Let's start with the fashion industry.
Matthew: A work called the "In Bloom" dress by X Y Z workshop Kae Woei and Elena Low are a couple in Melbourne, a couple of architects, and they bought a 3D printer just to sort of see what they could do with it. And they produced a bodice which they then took to Singapore for a 3-D printing show that was there and they won with their bodice. And so they were invited to then do a dress for a fashion show in New York and they produced this which was the "In Bloom" dress. And they wanted to create a long train and they had all these plans about what he wanted to do but they're printing with a printer that can only do little segments. And he had had quite a bit of trouble producing the panels and printing them so that they went into the right shape and modelling the panels he said was so hard he was beginning to think what's the point of doing 3-D printing if it's harder to do than if you just did it by hand.
And then he had a brainwave and went down to Spotlight which is the local fabric shop and bought one of the old fashioned paper patterns. And scanned the panels from the patterns which he could then manipulate in his CAD program and produced all the pieces that he needed for his dress.
Kai: So this was an intricate piece of work, a lot of work, many elements that had to be 3D printed. My question is Sandra if you wanted to wear this on a Friday night how early would you have to start printing this?
Sandra: What does Matthew think about that?
Matthew: You'd probably need to start about a month in advance. They're difficult to produce - it's slow producing things one at a time and in fact we had to send Kae Woei our mannequins. He said it's much easier for me to fit if the mannequin's here and I sent it back on the mannequin. So it's not really a practical solution, it's an experiment.
Kai: So this is an experiment, some of these things haven't gone very far. We can see what this technology will be able to do. But there are actual 3-D printed models on the market already such as a bikini.
Matthew: This is the first commercially available 3-D printed garment. And it's the N12 bikini. And personally I think they need to think a bit harder about the name. N12 refers to the nylon from which it's made. We basically ordered that and bought it for the collection and for the exhibition.
Sandra: So we've started off with one of 3-D printed things that go on the runway to commercially printed garments with 3D to now things we've never been able to do before.
Matthew: This is the kinematics petal dress from nervous systems. And this is printed in one go. This is printed in one piece. And if you look at the video here you can see that the model is moving and the dress flows like a piece of fabric. And yet if you look at these quite large pieces that make up the fabric the segments are big and in fact each segment is made of a triangular hinge system. So you've got hinges on all three sides. It's a spectacular piece of engineering is what it is. When it's printed in one go it's not printed lying flat but it's not printed standing up. It's printed folded. So the algorithm is able to compensate for the fold pattern. It determines the fold pattern for the dress that you want to put on. It's printed like that and then you can just shake it out. All you've got to do is get all the hinges moving and you're way.
Kai: So maybe you can print this at home or 10 15 years from now, who knows, we might be able to just print a dress straight onto the body on a Friday night and then leave for a party and then rip it off afterwards as a one off dress. Also this particular dress it's got these segments. If they were made from metal or titanium wouldn't that be a perfect dress for a Secret Service agent bullet proof and everything.
Sandra: So 3-D printing in fashion is not only about the material and the designs that we can make it is also about personalisation, is also about things like the military or applications beyond New York fashion runways. It's also about doing away with the idea of seasons or with the idea of brands. What if all of these designs are open source and we can access them anywhere anytime and print them in the comfort of our home.
Kai: And a new way of actually distributing dresses digitally online for printing at home or at the local print studio. Maybe there will be boutique print studios where you can have your fashion of choice printed to your liking in your material, your colour, so a whole new way of mass personalisation of fashion.
Sandra: So fashion was really a fascinating thing to explore. The next thing that's struck us as a significant development in how we think about what new manufacturing technologies can deliver was this idea that you could actually use 3-D printing to not only create buildings around you but also recreate the natural environment.
Matthew: This is a work by a local architect who works with an engineering company, James Gardiner, and he was interested in the creation of artificial reefs. So how do you create a substrate to build new coral reefs. We do try to build artificial reefs all the time. We usually do it by sinking boats or by throwing cars into the water or throwing tyres down but it's not a very good way of producing an artificial reef you can get some traction there but they tend to be monocultural or very low level of variety in the species and so they don't really take off as reef ecosystems. And he spent time talking to marine biologists and researching the subject and then designed a reef substrate and he printed a model for himself in plastic and it has a lot of different sized cavities and protuberances in order to get that sort of variety that would help establish an ecosystem. He then found a system of 3-D printing in sand that allowed him to make some test pieces. So this is a 3-D printed in sand coral reef substrate test sample, one of three that he had made. This one was put on the bottom of the ocean near Bahrain and was attracting a number of species of fish and other animals. Unfortunately they found out that the binding technology that holds the sand together eventually dissolves in the salt water and so the experiment came to an end. James is now designing new technologies actually for the company that he works for and looking at the potential to create structures like this or portions of that in concrete so that he can then stack at Lego-like so that he has this full reef in a substance that won't simply dissolve.
Kai: So as we've heard there are always teething problems. In innovation, the first iteration rarely ever does the trick. So you keep doing it and you experiment with different ways of doing it, different materials. So 3-D printing in sand is a good idea but if it dissolves it's not good for a reef. So you look with concrete and other materials. But I'm sure these things as we perfect them they will lead to something that will solve a real problem.
Sandra: So this is a great start that might help us rethink how we deal with coral bleaching and it is also a great start for how we might think of dealing with climate change. We could build reefs where we've never had reefs before like off the coast of Sydney in case the storms move south.
Kai: Our next topic is rocket science. Next we learn that there's some really great applications of 3-D printing with new materials such as titanium in rethinking and innovating traditional manufacturing processes. And the example at hand was a rocket engine.
Matthew: What we've got here is a 3-D printed jet engine from a company called Amaero in Victoria. It's made from a titanium alloy and it's quite small and it's quite light. But when I went down to talk to Amaero one of the things they told me about was that when they get companies saying we would like to produce one of these they offer a service which is we can do that for you but how would you feel if we were to take advantage of the materials, the strength of this centred metal powders to redesign that piece so that it actually really takes advantage of what this technology can do and what this material is capable of. So that ultimately the thing that you're trying to make is much lighter more powerful safer and they're having to offer that optimisation for free because people don't know that they want it. But for me there was was all a sort of excitement about 3-D printing about the possibility that you could print your own lunch or make something that you needed all of a sudden. And we saw lots and lots of little plastic knickknacks and things and I think people have expected to come to this exhibition and see plastic knicknacks and a printer printing which is marginally more interesting than watching paint dry. But I think what we haven't explored yet is the potential of both the printing technology, the new material and the capacity to do the digital design before you've done the printing. The whole lot has not really been pushed.
Sandra: So these new ways of manufacturing are going beyond just allowing us to do what we used to do but a little bit better or more efficiently or faster or more personalised.
Kai: Absolutely. We've discussed this previously on The Future, This Week podcast - when new technologies, transformation technologies, such as 3-D printing first appear, usually what you do is you're recreating what you've always done by new means but in the process you discover that you can do entirely new things that are transformative. So as this company has discovered it is not only able to print a jet engine in titanium via additive manufacturing, 3-D printing essentially, but they can actually now do digital designs and work on the efficiency of designs in ways that were never previously possible so they can use this 3-D modelling and that way of producing to create engines that are more efficient by orders of magnitude.
Matthew: Now that we can print in metals then that whole area opens up to us. I particularly love this one because I love the idea that for instance if we can print engines that are lighter, more powerful, use less fuel, hopefully make less noise. Then aviation may not be the disaster that it currently is for the atmosphere.
Sandra: So there are big promises that come with this technology with new ways of manufacturing with new ways of doing things with 3-D printing in general. But is this really such a new story?
Kai: I think there is something genuinely new about 3-D printing but as with any technology it always stands on the broad shoulders of the giants that have gone before. And so this exhibition has a section that looks at the history of the technology that preceded the current 3-D printing and new manufacturing technologies. And that tells us that some of those ideas have really been implemented far far earlier than we would commonly think.
Sandra: And we found this a really fascinating insight because even with our curiosity about the path of technology and with history in general on The Future, This Week, our podcast that we do, these were all developments that we have never heard about.
Kai: No, that's right.
Sandra: So they're invisible these giants.
Kai: And what is even more fascinating is that the pieces that are in the exhibition are actually in possession of the Powerhouse Museum so they duck into their own archives and were able to pull out these technologies and display them as part of this exhibition so let's listen to one or two in particular.
Matthew: Even though it's the latest great innovation it's actually based on a number of ideas that have been around for a very long time. And my experience is that a lot of great innovations are just older ideas that find a new context or new combinations. So over here we have a bust of a guy called Frederick Pollock. He was a Sydney based pharmacist. That portrait of him or that bust of him was produced using a photographic scanning technique whereby he sat on a stool on a special camera around him but it also knew the distance from the camera to him and the data in the film was used to generate a wax copy of his physique and then a bronze cast was made from the wax mould. So that was a service offered by a department store in Japan in 1934. Clearly it didn't take off. It's probably cheaper to get us somebody who could sculpt busts to do it for you but it predates what we now see as one of the great advantages of our digital scanning.
Kai: So this predates our current 3-D printing by a good 80 years. And neither of us have ever heard of it. No that's right. But there was a technology that was even older another hundred years before that in the early 1800's. So let's have a listen to that.
Matthew: This is a set of Jacquard cards that we have here. Joseph Marie Jacquard invented the automatic loom which uses punched cards to describe to his automatic looms what the pattern is that would be woven by them. And this stack of cards has a sample of the pattern that's woven by this particular code. Charles Babbage saw these when he was doing a research survey into manufacturing methods at the beginning of the 19th century. He was looking at the economy of manufacture generally on which he wrote a famous book called On The Economy of Manufacturers. But he also was interested in how he was going to build the engines that he had decided to build, his calculating engines, and for his analytical engine, this is the machine that would work like a computer, he wanted to be able to send new instructions to the machine as it was doing its calculations. And when he saw Jacquards cards he knew that there was a technology that would allow him to do what he wanted to do. Babbage was also something of a reformer and he was very influential and quite wealthy. Much easier to be influential when you're quite wealthy I think. So he would have big parties at his house on a Saturday afternoon and invite all the rich and famous people that he knew and the titled and well established in the government people along to his house. But he would also bring a lot of his scientific friends and artists along and they would be there not just to avail themselves of his fairly lavish offerings but he would deliver lectures to them and he would have his other friends give technical lectures so that people would engage in the new innovations of the day. And one of the things that he loved to do was to ask people to say how a portrait that he kept on his wall, this portrait, not this exact one but one of these exactly the same, he would say how was this produced? And it's a portrait of Joseph Marie Jacquard sitting in a chair. He's got his compass in his hand and he's marking out some cards there and it's quite an intricate portrait and you can see that it's got a window. You can see a view through the window and you can see there's a sort of transparent curtain across there. It's quite an amazing piece of work and Babbage's guests would go is it a drawing? Is it an etching? And eventually he would reveal that it is actually a silk weaving done from 24,000 Jacquard cards. And one of his guests the Duke of Wellington was so excited by it that he ran off and got Prince Albert, Queen Victoria's consort, to bring him back so that he could do the same thing to him. This is a digital weave. That's what it is. And it dates from about 1825. And we have this one. There are more than one because of course the cards were able to be used to reproduce them over and over. I love it. I love this work.
Sandra: And we loved it too didn't we? We sat about a metre away from this. And it basically looked like a black and white photograph.
Kai: Absolutely. It looked stunning. And you have to really go near it to see that it's actually made from fabric from cloth like a woven silk.
Sandra: From almost 200 years ago.
Kai: And the fascinating thing are the jacquard cards that are used to produce this with the automatic loom machine. It's really the first computing technology. It's very significant in the history of computing because it's the first time that data was stored in a digital way on what essentially were punch cards that later on became part of the first computer. And then in the 20th century were used by none other than International Business Machines (IBM) to create actual computing equipment that were able to store operations on these punch cards which is essentially what Jacquard did in 1825, storing operations was automatic machine on punch cards which are essentially digital, zeros and ones on these cards. Now it was not very efficient. He needed to use twenty four thousand of them but it is essentially 3-D printing because it's the storage of digital data that is then being turned into a physical object. So the principle was already there 200 years ago.
Sandra: So we absolutely love this exhibition because it takes you to the past, it takes it to the future and it allows you to reconsider not only what 3-D printing was and is, what its possibilities are, how it changes the way we think about industries, about our environment, about the materials that we use.
Kai: It has all the hallmarks of a truly transformative technology. We're yet to see where things will be going. The potentials are great. There's a long history as we've learned and we can't wait to see what else will happen with 3-D printing technology as we go forward. So why don't you go and check out this exhibition.
Sandra: Out of Hand: Materialising the Digital on the future of design and manufacturing at the Powerhouse Museum in Sydney.
Kai: Until the 18th of June 2017.
Sandra: Make sure to go see it.
Outro: You've been listening to Sydney Business Insights, the University of Sydney Business School podcast about the future of business. You can subscribe to our podcast on iTunes, SoundCloud or wherever you get your podcast and you can visit sbi@sydney.edu.au and hear our entire podcast archive, read articles and watch video content that explore the future of business.
Close transcript