Angela Hecimovic
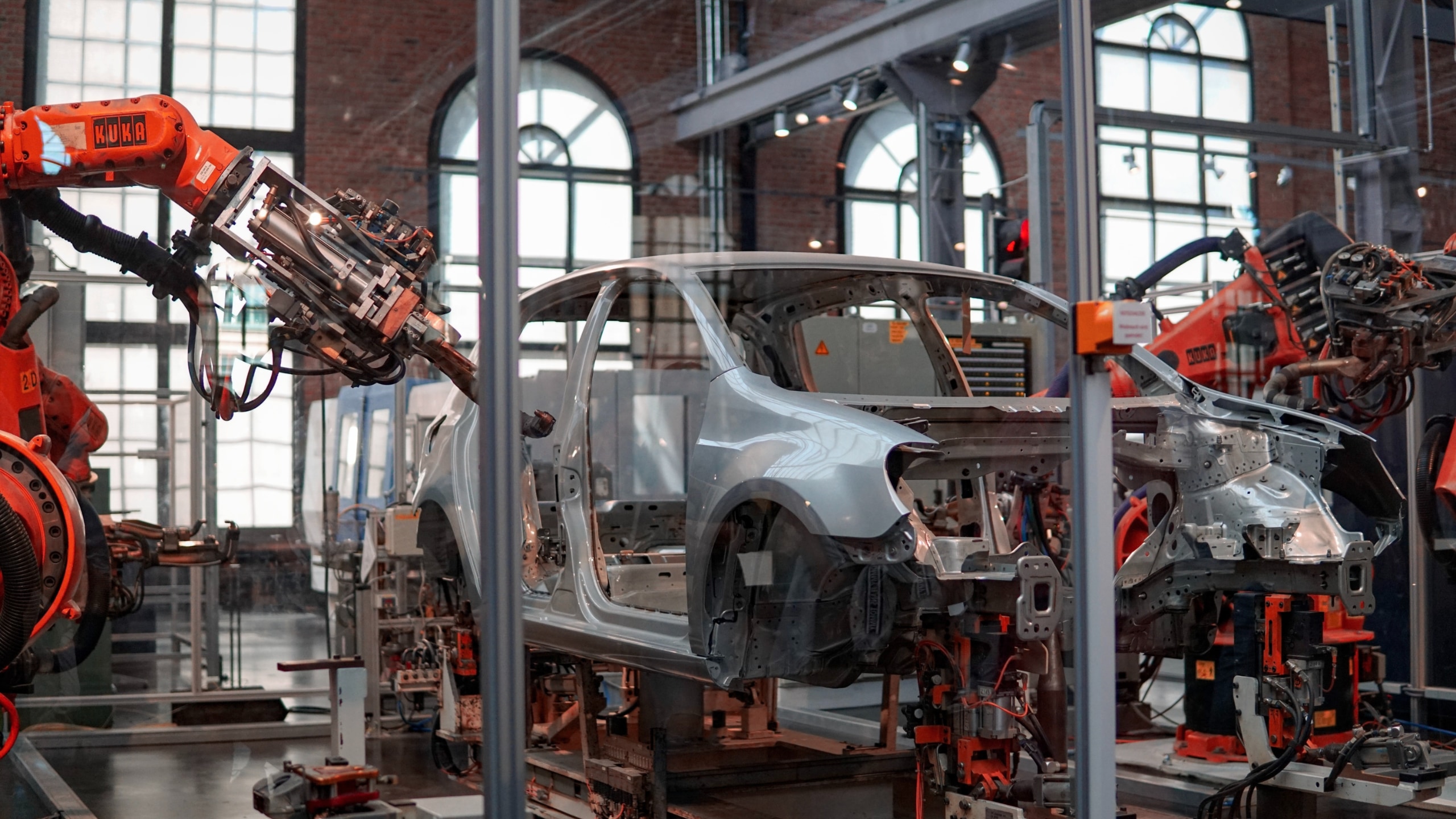
Keeping it local – the new supply chain vibe
Year long wait times for a new car is just one signal flashing the fragility of global supply chain arrangements and yes, my new Toyota will be here late 2023!
Increases in shipping costs, staff shortages and product delivery delays continue to disrupt supply chains as the pandemic grinds into a third year.
Frustrated manufacturers and businesses are questioning the underlying drivers of supply chain vulnerabilities, desperately seeking insights into building more resilient distribution processes. Our study set out to explore these drivers and offers some likely post-pandemic global supply chain scenarios.
Neoliberal globalisation – the supply chain back story
Long before the final product reaches consumers, its raw materials and intermediate input goods may have criss-crossed the globe multiple times. This multi-strand supply chain is the result of neoliberal globalisation policies, such as the reduction of trade barriers between nations, which emerged in the 1980’s.
These policies (with a special shout-out to the deregulation of capital markets) are why China and Southeast Asia became the world’s manufacturing hub. China has been the main beneficiary of global neoliberalism: currently it produces nearly 30% of manufactured goods, 50% of stainless steel and 80% of the printed circuit boards in smartphones and laptops.
Car manufacturing ended in Australia in 2019 as the industry was liberalised, with Southeast Asia now attractive with their low-cost labour and government incentives (lower taxes). However, my cousins in Geelong are still mourning the demise of Ford and blame the government’s minimal tariff protection policies.
Apple and other multinational firms have ‘offshored’ jobs from the Global North to the Global South facilitated by accounting and financial metrics that recognise the cheaper costs of labour, materials and inventory.
The West’s reliance on supply chains based in China is neatly demonstrated by the fall-off in the contribution of manufacturing to Australia’s GDP from almost 14% in 1990 to just 5% in 2020.
Australian Manufacturing Output 1990-2022
Building resilience into supply chains
China’s zero-COVID-19 policy continues to exacerbate shipment delays to western countries (note the severe production drop in 2020) and is forcing businesses to reassess the robustness of their supply chains.
Global neoliberalism is under attack from rising national populism, with nations like Australia venting concerns about reliance on other nation’s outputs and calls for greater degrees of onshoring and local manufacturing. As China increasingly seeks to influence geopolitical power relations and international trade, Western nations relying on a constant flow of goods from China are questioning the sustainability of existing supply chain structures.
Our study suggests accounting for more robust supply chains focused on risk management where strategic supply chain monitoring and enhanced visibility across all supplier tiers is essential to build resilience in business supply chains.
Supply chain’s new world order
We anticipate several scenarios may play-out post-pandemic including: (1) the resumption of the pre-COVID-19 status quo, (2) the shortening of supply chains with greater regionalisation, and (3) the re-emergence of onshoring in the Global North whereby supply chains either in part or in total are taken back within national borders.
“A new urgency in reducing greenhouse gases, and geopolitics, plus the war in the Ukraine, have put the fragility of global supply chains top of mind. As managers navigate this dynamic, they need to think beyond product costs and supplier choices”
Harvard Business Review, 2022
The likelihood is the future will contain traces of all three scenarios. Whichever trajectory emerges, it is clear that COVID-19 provides a reflection point for businesses and draws attention to ways to build greater resilience to global shocks.
Accounting for more robust supply chains
The professionalisation of supply-chain risk management varies considerably among companies, with many still adopting a reactive approach to supply-chain disruptions. Audits of procurement process will increase, as will digitisation of supply chains. AI generated reports, for example, could assist in identifying anomalies in patterns and supply chain processes, much like a continuous audit, where AI could predict supply chain vulnerabilities and assess capabilities, risk tolerance and contingencies. This will allow businesses to quickly adapt to disruptions and build-in redundancy.
Companies may need to rethink their views on risk, focusing on global developments that have potential supply chain repercussions. Organisations should prepare to acclimatise their business operations to a vastly different “post-globalisation” operating climate.
The pandemic is likely to fuel a growing shift for national manufacturing sovereignty – a reversal of 40 years of international trade practice and a rebuttal of global trade policy.
Expect to see performance measures such as resilience, re-configurability, and responsiveness in supply chain dashboards that have typically focused on more traditional KPIs such as cost, quality, and delivery. I know, resilience has become a saviour term, a panacea for all problems: in the evolving supply chain story it is the capacity of businesses to be more agile and mitigate supply chain disruptions. But by adopting new AI technologies that offer better real-time visibility, businesses can move beyond just mitigating supply chain risk, to enabling them to forecast, predict and respond swiftly to any future events that impact supply patterns. It might even land my longed-for Toyota sooner.
This is an overview of the author's article published online in the Accounting, Auditing and Accountability Journal.
Image: Lenny Kuhne
Angela is a Lecturer in the Discipline of Accounting at the University of Sydney Business School. Her research focus covers a range of audit and assurance issues aimed at improving our understanding of the assurance practice.
Share
We believe in open and honest access to knowledge. We use a Creative Commons Attribution NoDerivatives licence for our articles and podcasts, so you can republish them for free, online or in print.